CHAPTER 1
INTRODUCTION
1.1 Background
In the olden days, Nepal relied heavily on India for the supply of cement as there were no cement manufacturing industry in the country. Nepal’s first state owned cement manufacturing plant, Himal Cement Company Limited was established in 1967 A.D. After the massive earthquake that took place on 12th May – 2015; Nepal has set new standards for the construction of buildings. In cities like – Kathmandu, Biratnagar, Dharan, Butwal, Bhairawa, etc. high rise buildings and commercial complexes are being built-up by following new standards set by the government authorities. Since, there are high numbers of occupants in these types of buildings, it is very important to keep the quality of construction in priority as well as the construction cost into consideration.
Based on recent trends of construction, cost effectiveness is one of the most focused competitive strategies of the industry. Cost effectiveness focuses on operation efficiency for reducing the cost while quality remain constant.
1.2 Statement of Problems
For concreting works, the price of cement is very expensive in comparison with sand and aggregates. Cement is a complex material if it is not taken proper care then, its quality gets deteriorate with time and even gets as wastage when it comes in contact with moisture. Wastage of cement alone can over run the cost of the project. Therefore, the cost of cement is an important factor to be analyzed for the cost effective construction of any project. Currently, in Nepal, there are numbers of cement manufacturers like – Ghorahi, Jagdamba, Hetauda, Udaypur cements, etc. All of these manufacturers are producing 43 grade cement and some are even producing 53 grade of cement. Hence, it is the major job of the professionals to decide based on the market competitiveness to ensure the quality of cement by conducting various tests needed and the cost analysis. A research highlighting the issues of the quality of cement and suitability of price has not been conducted on local level yet; so this study is focused to analyze the quality of the cement and for the suitability of the cement brand considering the cost. M, S, A and SA cements have been analyzed in terms of their quality and suitability considering the cost as these three cement brands are only in construction works.
Abbreviations
OPC – Ordinary
Portland Cement
S – Shivam Cement
SA – Sagarmatha Cement
A – Aagni
M – Mangala
1.3 Project Objectives
The overall objective of the study was to assess the cost effectiveness of the applied cement brand with following specific objectives:
- To compare the quality of cement and cost of different brands of cements.
- To compare the cost difference among the different cement brands and analyze the impact on the costs of construction.
CHAPTER 2
LITERATURE REVIEW
Cement is a powdery substance made by calcining lime and clay, mixed with water to form mortar or mixed with sand, gravel and water to make concrete.
For construction purpose the meaning of the cement is restricted to bonding materials used with stones, sand, bricks, building blocks etc.
Following are the various applications of cement
- It is used in the cement mortar for masonry works, plastering, pointing etc.
- It is used for making joints for pipes, drains etc.
- It is used in concrete for laying floors, roofs and constructing beams, stairs, pillars etc.
- It is employed for manufacturing precast pipes, piles, fencing posts etc.
- It is used in construction of important engineering structures such as bridges, dams, tunnels, light houses etc.
- It is used in preparation of foundations, water tight floors, footpaths etc.
- It is applicable for construction of wells, water tanks, tennis courts, lamp posts, telephone cabins, roads etc.
Such type of project are evolving for the analysis of the cement to be used in construction. They must have certain given qualities in order to play its part effectively in a structure. When these properties recline within a certain range, the engineer is confident that in most of the cases the cement’s performance will be satisfactory. Also, based on these properties, it is possible to compare the quality of cement from different sources.
Table 1 shows the characteristics of different components that are used in manufacture of cement and also gives the information about the range within which these properties should recline.
Table 1: Characteristics of Components of Cement
S.N. | Characteristics | As per 53 Grade |
A | Chemical Characteristics | |
1 | LSF (Lime Saturation Factor) | 0.66-1.01 |
2 | AM (Alumina Modulus) | 0.669(min) |
3 | Insoluble Residue(% Mass) | 2%(max) |
4 | Magnesia (% Mass) | 6%(max) |
5 | Sulphuric Trioxide(SO3) | 3%(max) |
6 | Total Loss on Ignition | 4%(max) |
B | Physical Characteristics | |
1 | Specific Surface(CM^2/g) | 225m2/kg(min) |
2 | Setting time(minutes) | |
A | Initial Setting Time | Not less than 30 mins |
B | Final Setting Time | Not less than 600 mins |
3 | Soundness | |
A | By Le-Chataller(MM) | 10mm (max) |
B | By Auto clave (%) | 0.8%(max) |
4 | Compressive Test(N/mm^2) | |
A | 072±1hour; 3 days | 27MPa(min) |
B | 168±1hours; 7 days | 37MPa(min) |
C | 672±4hours; 28days | 53MPa(min) |
(NBC101:1994, 2064), (IS8112:1989, 2005), (IS12269:1987, 1988).
Among the characteristics that are mentioned in the table 1, only initial setting time, final setting time and soundness are used for the analysis.
2.1 Chemical and Physical Characteristics of Cement
- Lime Saturation Factor (LSF):
The Lime Saturation Factor is a ratio of CaO to the other three main oxides. Applied to clinker, it is calculated as: LSF = CaO/(2.8SiO2+1.2Al2O3+0.65Fe2O3) Where, CaO = Lime, SiO2 = Silica, Al2O3 = Alumina and Fe2O3 = Iron oxide Often, this is referred to as a percentage and therefore multiplied by 100. The LSF controls the ratio of aliteto belitein the clinker. A clinker with a higher LSF has a higher proportion of alite to belite than a clinker with a low LSF. Typical LSF values in modern clinkers are 0.92-0.98 or 92% – 98%. The Lime saturation factor has a great role on the compressive strength of the cement. If this factor exceeds the margin (90-98%) then, large clusters of belite are present in the clinker that adverse the grinding of the clinker (Ibrahimi, Jamaa, Bagane, Ammar, Lecomte, & and Diliberto, 2015). According to Nepal Standard (N.S) and Indian Standard (I.S) the lime saturation factor can be in the range 0.66 –1.02.
- Alumina Modulus (AM):
It shows the factor or ratio or proportion of iron oxide and alumina. It was also called alumina ratio. Alumina Modulus = Al2O3/Fe2O3 Values of alumina ratio are in the range from 1.5 to 2.5.The AR determines the composition of liquid phase in the clinker, when it’s lower than 1.5 both oxides are present in their molecular ratios and therefore only tetra calcium alumino ferrite can be formed in the clinker; consequently, the clinker cannot contain tricalcium aluminate. This is the case called Ferrari-cement which is characterized by low heat of hydration, slow setting and low shrinking. A high alumina ratio together with a low silica ratio results among other things, in a fast setting of the cement; this requires the addition of a higher gypsum rate to control the setting time. However, the limitation set by Nepal standard and Indian standard for Alumina modulus is minimum 0.66.
- Insoluble Residue:
Insoluble residue is a non – cementing material which is present in Portland cement. This residue material affects the properties of cement, especially its compressive strength. To control the non – cementing material in Portland cement, American Society for Testing and Materials (ASTM) allows the insoluble residue to be nothing more than 0.75%.This limitation is much lower than the allowance provided by the British standard which is 1.5%. However, the limitation set by the
Nepal standard early age and the figure was also found to be reduced as the cement mortar was older with 7.28% of insoluble residue in the mortar at 1 day, the compressive strength was reduced by 11.5%, but after 60 days, the strength of the same mortar was only reduced by 5.5% as compared to the control mortar. It was also found that the compressive strength of Portland cement mortar with insoluble residue provided by ASTM standard or British standard was still higher than the compressive strength of Portland cement mortar type I allowed by the standards. The limit of insoluble residue given by ASTM standard as 0.75 is rather low and can possibly be increased to 1.5% according to British standard, or even slightly higher, without significantly reducing the compressive strength of cement.
- Magnesia (MgO):
Magnesium hydroxide occupies more volume and puts stress on the hardened concrete. This leads to cracks in the concrete structure. As time goes by, these cracks grow deeper, causing leakages or irreparable damage to the structure. Magnesia is one of the major culprits behind late expansion cracks in concrete. Due to formation of expansion cracks in concrete due to volume expansion of magnesia, the durability of concrete will be very poor. MgO in excess of about 2% appears in the clinker as free MgO. MgO present 1-1.5% in clinker is a very good mineralizer and improves nodulation. If it is quenched it does not give expansion problems. Good nodules are always preferred in burning and it helps in improving cooling efficiency and there by recovering thermal energy from clinker. Within the kiln MgO increases the liquid phase and may therefore promote the formation of clinker minerals. However, too much MgO can increase the liquid phase to problematic amounts and cause excessive coating and even balling of the clinker. MgO at about 2-5% can improve the burn ability of raw mill, promote the absorption of free lime, increase the strength development of cement and shorten the setting time.
- Sulphuric Trioxide(SO3):
To control setting time effectively, cement needs a minimum amount of calcium sulfate, mostly in the form of gypsum added to the clinker. As per N.S and I.S, the maximum allowable SO3– content in the cement is 3% to prevent sulfate expansion. It was reported that increasing the SO3 content above 3.0% had negative effects on durability assessed by strength or expansion measurements.
- Total Loss on Ignition(LOI):
Ignition loss (LOI) represents the % weight loss suffered by a sample of cement after heating to 900 – 1000°C (1650 – 1830°F). Any water bonded to hydrated cement particles is expelled above this temperature. The higher the LOI, the less strength the cement will develop. As an indicator it can be used to monitor and improve the quality of the final cement.
N.S and I.Slimit the LOI to maximum 4.0%.
- Specific Surface Area(S.S.A):
Specific surface area of a porous material is defined as the surface area of pores per unit mass or per unit bulk volume of the porous material. For two materials with the same total pore volume, the material with fine pores has a much greater specific surface area than the material with large pores. It is given by the following equation: S.S.A = As / Vb or, S.S.A = As / m Where, As = total surface area of the pores, Vb = bulk volume of the material, and m = mass of the material (Aligizaki, 2006) Cement fineness is expressed in terms of Particle Size Distribution (PSD) with residues (or passing) on reference sieves or by its specific surface area in Blaine. There are three methods commonly in use at present time to determine the S.S.A. They are Blaine Air Permeability Method, Lea and Nurse Air Permeability, and Wagner Turbidity Meter. Specific surface is expressed as the total surface area in square meters of all the cement particles in one kilogram of cement. The higher the specific surface area, the cement is said to be finer. The size of a cement particle has an important effect on the rate at which it will hydrate when exposed to water. As it reacts, a layer of hydration product forms around the outside of the particle, separating the unreacted core of the particle from the surrounding water. As the layer grows thicker, the rate of hydration slows down. Therefore, a small particle will react much more quickly than a large particle.
- Setting Time:
Cement when mixed with water forms paste which gradually becomes less plastic, and finally a hard mass is obtained. In the process of setting, a stage is reached when the cement paste is sufficiently rigid to withstand a definite amount of pressure. The time to reach this stage is termed as setting time.
Setting time is divided into two types:
- Initial Setting Time – The time at which the cement paste loses its plasticity is termed as the initial setting time.
- Final Setting Time – The time taken to reach the stage when the paste becomes a hard mass is known as the final setting time. For an OPC, the initial setting time should not be less than 30 minutes and final setting time should not be more than 600 minutes. In practice, the length of time for which a concrete mixture will remain plastic is usually more dependent on the amount of mixing water used and atmospheric temperature than on the setting time of cement.
- Soundness
The change in the volume of hardened concrete due to delayed or slow hydration of free lime, magnesia and calcium sulfate present in cement is known as unsoundness. It causes undesirable stresses resulting in cracks. It is essential that concrete does not undergo a large change in volume after it has set. The tests for unsoundness are the Le Chatelier and Autoclave tests. According to N.S and I.S, the expansion carried out should not be more than 10 mm in the Le Chatlier test and 0.8% in Autoclave test.
- Compressive Strength:
Cement mortar cubes (1:4) having an area (150*150) mm2are prepared and tested in compression testing machine. Standard sand (IS: 650) is used for the preparation of cement mortar.
- Consistency test
This test is conducted to determine the percentage of water required for preparing cement paste of standard consistency for various tests. This test is performed by vicat’s apparatus. The standard consistency value ranges from 33%to35%.
- Fineness test:
The objective of conducting this test is to check the proper grinding of cement as finer cements has quicker action with water and gain early strength.
Finer the cement, more surface area of the aggregate covered by it. The fineness of cement is tested by sieve test. The standard value of fineness ranges from 6% to 10%.
2.2 Workability
Good cement possesses the following properties (which depends upon its chemical composition, thoroughness of burning and fineness of grinding).
- Provides strength to the masonry.
- Stiffens and hardens early.
- Possesses good plasticity.
- An excellent building material.
- Easily workable.
- Good moisture resistant.
CHAPTER 3
METHODOLOGY
This research is limited to the cost and quality comparison of different brands of cement found around Kathmandu Valley. The research was focused to assess the cement cost and quality by comparing the cement in terms of their quality and price. All the data required were taken from the different websites mentioned in the reference section.
3.1 Data Collection
The required data were collected from the following source:
- Secondary source:
Data for various tests such as setting time, fineness, consistency and compressive strength of cement were taken from different websites on selected brands of cement to evaluate the qualitative properties of cement. Various publications, reports and standard codes set by Nepal and India related with the research objectives were studied and reviewed. The publications, reports, and standard codes were taken from libraries and internet.
Table 2: Cost comparison of different brands of cement
The table shown below gives the information about the cost per kg of different brands of cement available in the market of Kathmandu valley.
S.N. | Particulars | Price per 50 kg bag | Price per kg |
1 | Shivam Cement | Rs. 820 | Rs. 16.4 |
2 | Sagarmatha Cement | Rs. 750 | Rs. 15 |
3 | Agni Cement | Rs. 740 | Rs. 14.8 |
4 | Mangala Cement | Rs. 730 | Rs. 14.6 |
3.2 Lab Tests on Cement
For Physical Properties
- Setting Time of Cement
Vicat’s apparatus is used to find the setting times of cement i.e., initial setting time and final setting time.
- Initial Setting Time
- For this test, a needle of 1 mm square size is used. The needle is allowed to penetrate into the paste.
- The time taken to penetrate 33-35 mm depth is recorded as the initial setting time.
- Final Setting Time
- For determining the final setting time, the needle of the Vicat’s apparatus was replaced by the needle with an annular attachment.
- The time (t3) was recorded when the annular attachment failed to make an impression on the surface of the test block.
- Results
Initial setting time = t2-t1
Final setting time= t3-t1,
Where,
t1=Time when water was added to cement.
t2=Time when needle failed to penetrate 5 mm to 7 mm from bottom of the mould.
t3=Time when the needle made an impression but the attachment failed to do so.

2. Compressive Strength
Cement mortar cubes (1:4) having an area (150*150) mm2 were prepared (i.e. three cubes of cement) and tested in compression testing machine. The compressive strength at 7 days was found out.
Procedure:
2kg of different brands of cement was added and 4 kg of sand was added and 8 kg coarse aggregate was mixed together and tested for 7 days.
The second day of testing cement cubes was kept in water and was taken out from cube box.
Table 3: Assumed cubes sizes
Grade of conc. | Cement | Fine sand | Coarse sand | W/C ratio maximum |
M15 | 1 | 2 | 4 | .64 |
3. Consistency test:
300 gm of cement was taken and approximately 35% of water was mixed in various brands of cement and the consistency was determined and the initial and final readings were noted. In this test plunger needle was used.
4. Fineness test:
100 gm of cement was taken and was shaken for 10 minutes. The fineness of the cement was taken by measuring the weight of residue in laboratory. This process is done by sieve analysis process.
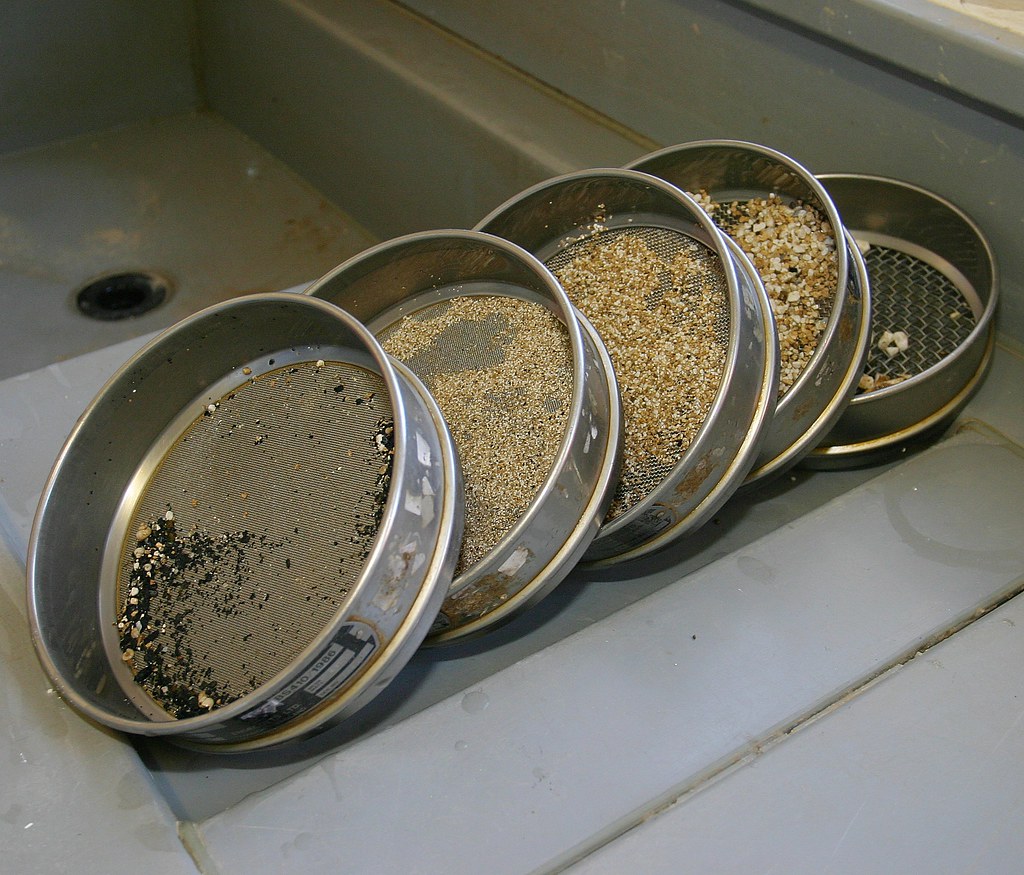
Fig 3: 90 micron sieve
3.3 Cost Analysis
Cost analysis was done by:
- Based on purchase: – First of all, the market price of cement per bag was tabulated. Then, the transportation cost to site from market was kept in consideration.
- Based on quality: – All the performed tests showed the result of quality of cement based on consistency, fineness, setting time, compressive strength which helps in making the construction in low cost.
CHAPTER 4
RESULTS AND DISCUSSION
A, M, S and SA cements were analyzed by the data taken from secondary source and the results were concluded as below:
Table 4 give the information about the quantity of water added to the cement and the initial setting time of the cement.
Table 4: Initial test
S.N. | Quantity of cement | Water added (ml) | Brands of cement | Time taken (in mins) | Result | Remarks |
1. | 300 gm | 81.6 | A | 36 | 5 | Fail |
2. | 300 gm | 89.25 | S | 45 | 6 | Pass |
3. | 300 gm | 76.5 | SA | 48 | 6 | Pass |
4. | 300 gm | 84.5 | M | 64 | 4 | Fail |
Form Vicat apparatus test and the results obtained from the test we conclude that Shivam Cement & Sagarmatha Cement has the best initial setting time.
Table 5 gives the information about the compressive strength for the cement mortar cubes of different brands of cement.
Table 5: Compressive strength test
S.N | Brands of cement | Days | Average weight (kg) | Compressive Strength ( N/mm2) | Remarks |
1. | A | 7 | – | – | – |
2. | S | 7 | 12000 | 5.3 | Very good |
3. | SA | 7 | 9000 | 4 | Good |
4. | M | 7 | 4500 | 2 | Very poor |
From the above test Shivam cement has highest compressive strength than the other brands of cement so we conclude Shivam cement is best.
Table 6 gives the information about the fineness test for the cement.
Table 6: Fineness Test
S.N. | Brands of cement | Time Duration (mins) | Fineness Percentage | Remarks |
1 | A | 10 | 8% | Good |
2 | S | 10 | 7% | Good |
3 | SA | 10 | 10% | Good |
4 | M | 10 | 12% | Poor |
From the above table, we can conclude that among those brands of cement Shivam has the least fineness percentage so Shivam is the best.
Table 7 shows the consistency of different brands of cement
Table 7: Consistency test
S.N | Brands of cement | Weight of cement taken (in gm) | Water added to design mix(in ml) | Final consistency | remarks |
1. | A | 300 | 96 | 33 | good |
2. | S | 300 | 105 | 33 | good |
3. | SA | 300 | 90 | 30 | poor |
4. | M | 300 | 99 | 32 | poor |
From the above table, Shivam cement has the greater final consistency. So, Shivam cement is best among those.
Source: https://www.researchgate.net/publication/330542459_Quality_Assessment_of_Cements_of_Nepal
CHAPTER 5
CONCLUSION AND RECOMMENDATIONS
5.1 Conclusion:
From the secondary sources, we found that Shivam cement is best cement and the most popular brand of cement used for construction purposes in Kathmandu valley.
Among the four brands of cement, that were taken into consideration for this project Shivam cement has good remarks in terms of every test whereas Mangala cement had very poor results. Although Sagarmatha and Aagni showed satisfying results. From the cost comparison table we can clearly see that Mangala is cheaper and Shivam is more expensive among them.
5.2 Recommendations:
Quality of cement is most essential things in construction. So, keeping the quality into consideration Shivam cement is best as it gives quality although its cost is high. For long life span of any civil engineering projects, Shivam cement is most recommended as it gives best quality than other brands of cement
References:
- AligizakiK. Definition of Pore Structure parameters.2006. In K. Aligizaki, Pore Structure of Cement-Based Materials Testing, Interpretation and Requirements (p. 19). Taylor and FrancisGroup.https://www.highwayguide.co.in/compressive-strength-test-of-cement-mortar-cube-as-per-is-4031-part-6/Association of Engineers. Reduction of Strength of Cement. In Civil Engineer’s Hand Book. 1981Kerala: Kerala Public Works Department
- NBC101:1994. (2064). NS 49/2041 Ordinary Portland Cement. Department of Building, Urban Development and Building Construction. Kathmandu: Government of Nepal Physical Planning and Works.
- Winter N. (2005). Understanding Cement – Interpreting Cement Science Since 2005. (WHD Microanalysis Consultants Ltd.) Retrieved December 04, 2017, from Understanding Cement – Interpreting Cement Science Since 2005: https://www.understanding-cement.com/parameters.html#
- Er. R.K Rajput, 2000,”Engineering materials”, 4th revised edition 2010, S.Chand.
- Prof. Prabin Singh, 1965, “Civil Engineering Materials”, 6th edition 2013, S.K Kataria andSons.
- Mishra AK, Regmi U. Effects of Price Fluctuationon the Financial Capacity of “Class A” Contractors.International Journal of Creative Research Thoughts 2017